Aluminum Straight Shank Milling Cutter
Product Size
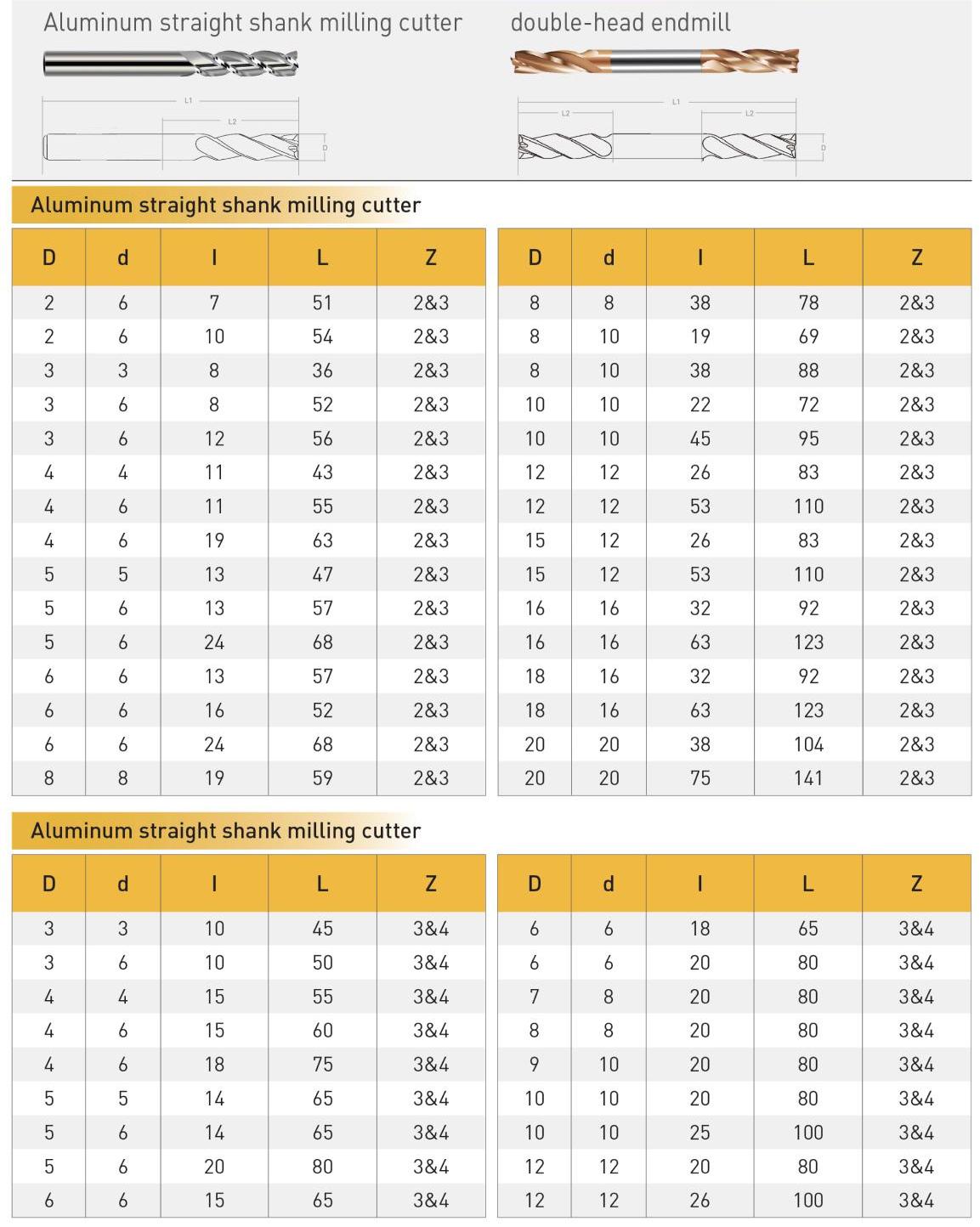
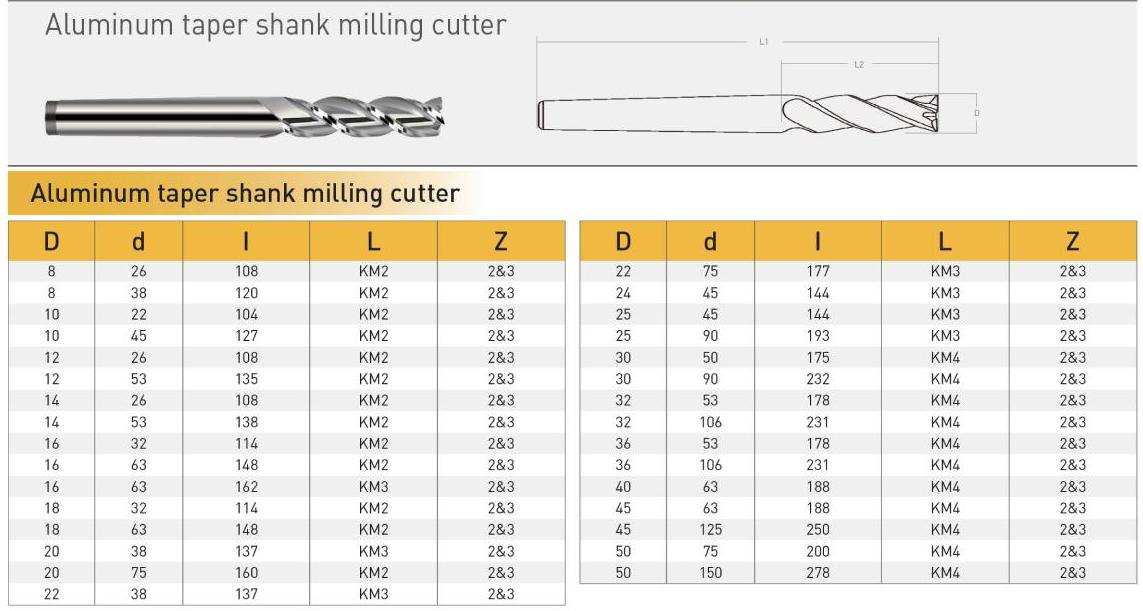
Product Description
The heat resistance of milling cutters is also one of its key properties. During the cutting process, the tool generates a large amount of heat, especially when the cutting speed is high, the temperature will rise sharply. If the heat resistance of the tool is not good, it will lose its hardness at high temperatures, resulting in a decrease in cutting efficiency. Our milling cutter materials have excellent heat resistance, meaning they retain high hardness at high temperatures, allowing them to continue cutting. This property of high-temperature hardness is also called thermohardness or red hardness. Only with good heat resistance can the cutting tool maintain stable cutting performance under high temperature conditions and avoid tool failure due to overheating.
In addition, erurocut milling cutters also have high strength and good toughness. During the cutting process, the cutting tool needs to withstand great impact force, so it must have high strength, otherwise it will easily break and be damaged. At the same time, because milling cutters will be impacted and vibrated during the cutting process, they should also have good toughness to avoid problems such as chipping and chipping. Only with these properties can the cutting tool maintain stable and reliable cutting capabilities under complex and changeable cutting conditions.
When installing and adjusting the milling cutter, strict operating steps must be taken to ensure the correct contact and cutting angle between the milling cutter and the workpiece. This not only helps improve processing efficiency, but also avoids workpiece damage or equipment failure caused by improper adjustment.